Full Cost Fc Method Definition
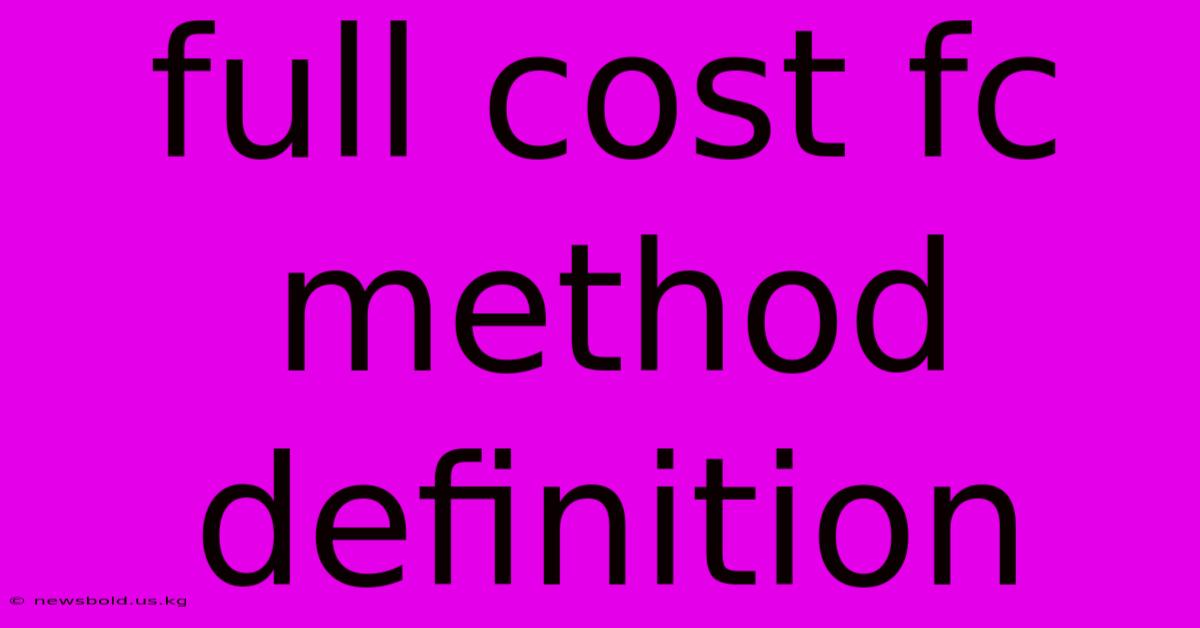
Discover more in-depth information on our site. Click the link below to dive deeper: Visit the Best Website meltwatermedia.ca. Make sure you don’t miss it!
Table of Contents
Unveiling the Full Cost FC Method: A Comprehensive Guide
What is the true cost of a product, and how accurately can it be determined? The full cost (FC) method, also known as absorption costing, provides a robust approach to cost accounting, offering a more complete picture of product pricing than alternative methods. This comprehensive guide explores the full cost FC method definition, its applications, and its limitations.
Editor's Note: This comprehensive guide to the Full Cost FC Method has been published today.
Why It Matters & Summary: Understanding the full cost FC method is crucial for businesses seeking accurate product pricing, informed decision-making, and improved profitability. This guide provides a detailed explanation of the method, its components (direct materials, direct labor, manufacturing overhead), and its advantages and disadvantages. Keywords include: full cost method, absorption costing, cost accounting, product costing, cost allocation, overhead costs, profitability analysis, pricing strategy, cost-volume-profit analysis.
Analysis: This guide synthesizes information from established cost accounting literature and real-world applications. The analysis focuses on clearly explaining the complexities of the full cost method, enabling readers to understand its practical implementation. Examples are provided to clarify the concepts and aid understanding.
Key Takeaways:
Point | Description |
---|---|
Definition | Assigns all manufacturing costs (direct and indirect) to products. |
Components | Direct materials, direct labor, and manufacturing overhead. |
Allocation | Overhead costs are allocated based on a predetermined overhead rate. |
Advantages | Provides a more complete product cost, facilitates better pricing decisions, aids in inventory valuation. |
Disadvantages | Can be complex to implement, may not be suitable for all businesses (e.g., those with diverse product lines). |
Applications | Pricing decisions, inventory valuation, performance evaluation, cost-volume-profit analysis. |
Let's delve into the intricacies of the full cost FC method.
Full Cost FC Method: A Deep Dive
The full cost FC method, in its essence, is a costing method that assigns all manufacturing costs – both direct and indirect – to the products produced. Unlike variable costing, which only includes variable manufacturing costs, the full cost method considers all relevant costs. This comprehensiveness offers a more complete picture of the cost of producing a product.
Key Aspects of the Full Cost FC Method
- Direct Materials: These are the raw materials that directly become part of the finished product (e.g., wood for furniture, fabric for clothing). Their cost is easily traceable to each unit.
- Direct Labor: This represents the wages and salaries paid to employees directly involved in the production process (e.g., assembly line workers, machinists). This cost is also directly traceable.
- Manufacturing Overhead: These are indirect costs associated with the manufacturing process that are difficult to directly trace to individual units. Examples include factory rent, utilities, depreciation of factory equipment, and indirect labor (e.g., supervisors). The challenge lies in accurately allocating these costs to individual products. This typically involves a predetermined overhead rate based on a chosen cost driver (e.g., machine hours, direct labor hours).
Discussion: Allocating Manufacturing Overhead
The allocation of manufacturing overhead is a critical aspect of the full cost FC method. An inaccurate allocation can significantly distort product costs and lead to flawed decision-making. Several methods exist for allocating overhead, including:
- Plantwide Overhead Rate: This simple method uses a single overhead rate for the entire factory, based on a single cost driver. It is straightforward but may be less accurate than other methods, especially in companies with diverse products or processes.
- Departmental Overhead Rates: This method uses separate overhead rates for each department within the factory, offering a more precise allocation than the plantwide rate. This is particularly useful in companies with distinct departments with varying overhead cost structures.
- Activity-Based Costing (ABC): This sophisticated method assigns overhead costs based on specific activities involved in the production process. While more accurate, it is also more complex and costly to implement.
The choice of overhead allocation method depends on the complexity of the manufacturing process, the diversity of products, and the desired level of accuracy.
Exploring Key Aspects: Direct Costs and Overhead Allocation
Direct Costs: The Foundation of Product Costing
Direct costs – direct materials and direct labor – form the bedrock of the full cost FC method. Their traceability simplifies the cost assignment process. However, accurate measurement and tracking of these costs are still essential for reliable product costing. Any inaccuracies in recording these costs will directly impact the final product cost calculation. The importance of accurate inventory management and payroll systems is undeniable in ensuring the correct determination of direct costs.
Overhead Allocation: A Critical Challenge
The allocation of manufacturing overhead presents a more significant challenge. Because overhead costs are indirect, their assignment to individual products requires a predetermined overhead rate. The selection of an appropriate cost driver is critical. If the chosen cost driver does not accurately reflect the consumption of overhead resources by different products, the cost allocation will be distorted. This can lead to inaccurate product costs and flawed pricing decisions. For instance, if machine hours are used as the cost driver but one product requires significantly more machine time than another, using a plantwide rate may misrepresent the true overhead cost of each product.
The Relationship between Overhead Allocation and Product Pricing
The accuracy of overhead allocation directly impacts the product's final cost and, consequently, its selling price. An under-allocation of overhead costs can lead to underpricing, potentially resulting in losses. Conversely, an over-allocation can lead to overpricing, making the product less competitive. The selection of an appropriate allocation method and cost driver is therefore crucial for sound pricing strategies and profitability.
Addressing Challenges and Limitations
While the full cost FC method offers a more comprehensive view of product costs, it is not without its limitations. One significant challenge is the allocation of fixed overhead costs. Fixed overhead costs, such as rent and depreciation, do not change with production volume. However, the full cost method assigns these costs to products, potentially distorting costs, especially during periods of low production. This can lead to inaccurate product cost figures and negatively influence managerial decision-making.
Another limitation is the complexity of implementation, particularly in companies with diverse product lines or complex manufacturing processes. The more complex the process, the more intricate and time-consuming the overhead allocation process becomes. This complexity requires significant resources and expertise in cost accounting.
Frequently Asked Questions (FAQ)
Introduction: This section addresses common questions regarding the full cost FC method.
Questions and Answers:
-
Q: What is the difference between the full cost method and variable costing? A: The full cost method includes all manufacturing costs (direct and indirect) in product costing, while variable costing only includes variable manufacturing costs.
-
Q: How is the predetermined overhead rate calculated? A: It's calculated by dividing the estimated total manufacturing overhead costs by the estimated total amount of the chosen cost driver (e.g., machine hours, direct labor hours).
-
Q: Why is accurate overhead allocation crucial? A: Inaccurate allocation leads to distorted product costs, influencing pricing decisions and profitability analyses.
-
Q: What are the limitations of the full cost method? A: Complexity of implementation, potential distortion of costs during periods of low production, and the difficulty in allocating fixed overhead costs.
-
Q: Is the full cost method suitable for all businesses? A: No, it may not be suitable for businesses with highly diverse product lines or complex manufacturing processes where other methods may provide more accurate costing.
-
Q: How does the full cost method affect inventory valuation? A: It's used to determine the value of finished goods inventory, which impacts the financial statements.
Summary: Understanding the nuances of overhead allocation is paramount for accurate application of the full cost method.
Transition: Let's now consider some practical tips for implementing this method effectively.
Tips for Implementing the Full Cost FC Method
Introduction: Successful implementation of the full cost FC method requires careful planning and execution.
Tips:
- Accurate Cost Data Collection: Implement robust systems for tracking direct materials, direct labor, and manufacturing overhead costs.
- Appropriate Cost Driver Selection: Choose a cost driver that accurately reflects the consumption of overhead resources by different products.
- Regular Overhead Rate Review: Periodically review and update the predetermined overhead rate to ensure accuracy and reflect changes in cost structures.
- Process Simplification: Streamline the allocation process to reduce complexity and improve efficiency.
- Software Utilization: Utilize cost accounting software to automate calculations and improve accuracy.
- Cross-Functional Collaboration: Ensure effective collaboration between production, accounting, and management teams.
Summary: Implementing these tips ensures a smoother and more accurate application of the full cost FC method, leading to better business decisions.
Transition: Let's summarize our exploration of the full cost FC method.
Summary of the Full Cost FC Method
This guide provided a comprehensive analysis of the full cost FC method, examining its definition, components, applications, and limitations. The allocation of manufacturing overhead, a critical aspect of the method, was thoroughly discussed, highlighting its impact on product costing and pricing decisions. The challenges and limitations of the method were also addressed, underscoring the importance of careful implementation and consideration of alternative costing methods where appropriate.
Closing Message: Mastering the full cost FC method is essential for businesses aiming to achieve accurate product costing and sound financial management. By understanding its nuances and applying effective implementation strategies, businesses can utilize this method to improve profitability and make informed decisions. The continuing evolution of cost accounting techniques necessitates ongoing professional development to remain abreast of the best practices and adaptations relevant to one's specific business needs.
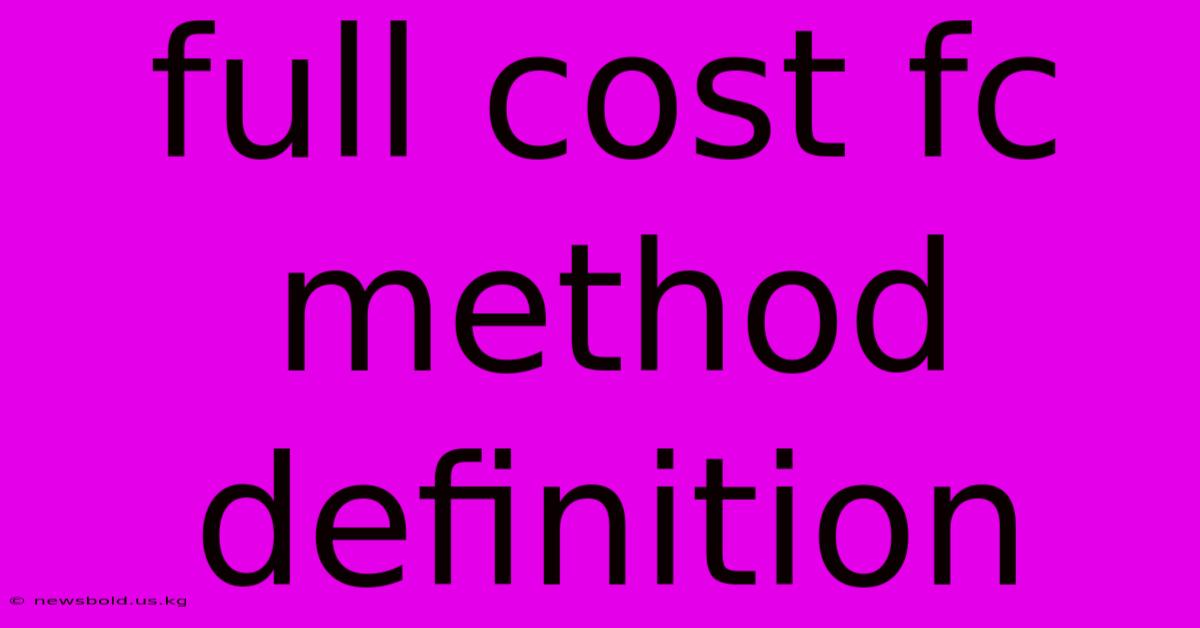
Thank you for taking the time to explore our website Full Cost Fc Method Definition. We hope you find the information useful. Feel free to contact us for any questions, and don’t forget to bookmark us for future visits!
We truly appreciate your visit to explore more about Full Cost Fc Method Definition. Let us know if you need further assistance. Be sure to bookmark this site and visit us again soon!
Featured Posts
-
What Is A Graphics Processing Unit Gpu Definition And Examples
Jan 05, 2025
-
Greenmail Definition How It Works Example Legality
Jan 05, 2025
-
How Does Pension Affect Social Security
Jan 05, 2025
-
Initial Interest Rate Cap Definition
Jan 05, 2025
-
Hard Landing Definition
Jan 05, 2025