Manufacturing Resource Planning Mrp Ii Definition And Example
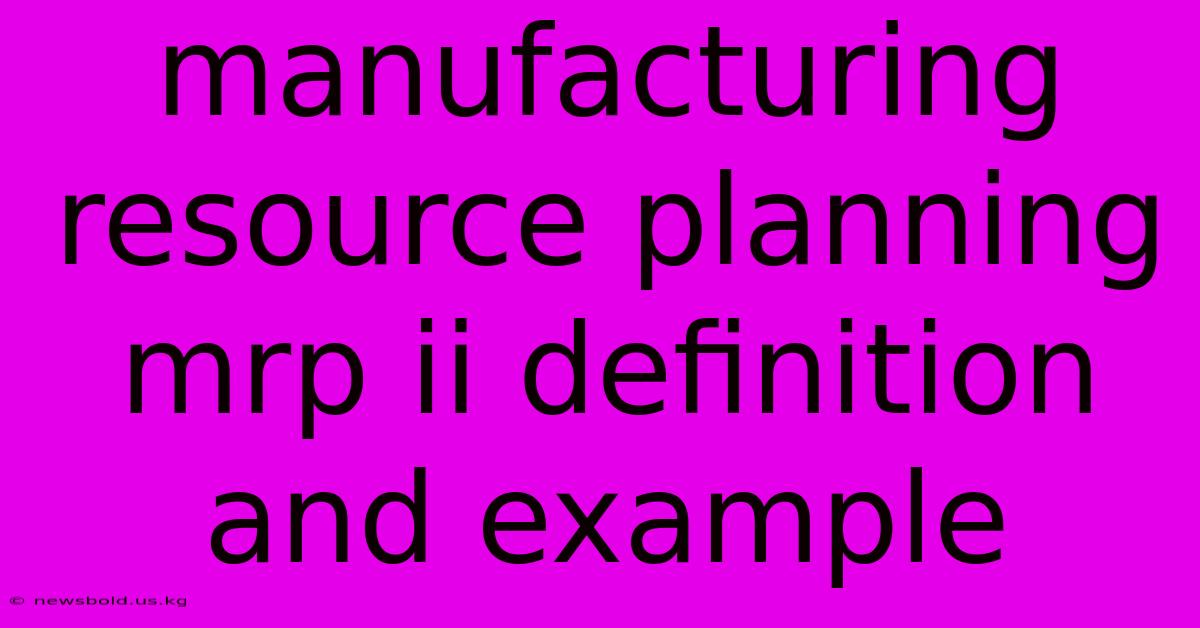
Discover more in-depth information on our site. Click the link below to dive deeper: Visit the Best Website meltwatermedia.ca. Make sure you don’t miss it!
Table of Contents
Unlocking Manufacturing Success: A Deep Dive into MRP II
Does your manufacturing process feel like a chaotic puzzle, with parts missing and deadlines constantly missed? A robust system is crucial for efficiency and profitability. This article explores Manufacturing Resource Planning (MRP II), revealing its definition, implementation, and transformative potential.
Editor's Note: This comprehensive guide to Manufacturing Resource Planning II (MRP II) was published today.
Why It Matters & Summary
MRP II is a crucial planning system for manufacturers seeking to optimize resource allocation, streamline production, and enhance profitability. This guide provides a detailed analysis of MRP II, covering its definition, core components, implementation steps, benefits, and limitations. It delves into real-world examples, illustrating its practical applications and addressing common challenges. Relevant semantic keywords include: Materials Requirements Planning, production planning, inventory management, capacity planning, demand forecasting, enterprise resource planning (ERP), supply chain management, manufacturing execution systems (MES), lean manufacturing, and just-in-time (JIT) inventory.
Analysis
This analysis of MRP II draws upon extensive research across academic literature, industry best practices, and case studies from diverse manufacturing sectors. The aim is to provide a clear, actionable understanding of MRP II, enabling manufacturers to assess its suitability and potential within their own operational contexts. The information presented is structured to guide readers through a systematic evaluation of MRP II's capabilities and limitations, helping them make informed decisions about implementation and optimization.
Key Takeaways
Key Aspect | Description |
---|---|
Definition | An integrated system for production planning and resource management. |
Core Components | Demand forecasting, master production schedule, materials requirements planning, capacity requirements planning |
Implementation Steps | Data collection, system selection, process mapping, training, testing, and ongoing optimization. |
Benefits | Reduced inventory costs, improved on-time delivery, increased efficiency, better resource utilization. |
Limitations | Data accuracy dependency, system complexity, initial investment costs, potential integration challenges. |
Manufacturing Resource Planning (MRP II): A Detailed Exploration
MRP II is a sophisticated planning and control system designed to manage all resources required for manufacturing—materials, labor, and machinery. Unlike its predecessor, Materials Requirements Planning (MRP), which focuses solely on materials, MRP II takes a holistic approach, encompassing all aspects of production, from demand forecasting to final product delivery.
Key Aspects of MRP II
- Demand Forecasting: Accurately predicting future customer demand is paramount. Various forecasting techniques, like moving averages and exponential smoothing, are used to generate a reliable sales forecast. This forecast forms the foundation of the entire MRP II plan.
- Master Production Schedule (MPS): The MPS translates the sales forecast into a detailed production plan, specifying the quantity and timing of each product to be manufactured. This schedule considers factors such as production capacity, lead times, and inventory levels.
- Materials Requirements Planning (MRP): MRP calculates the precise quantities and delivery times for all raw materials, components, and subassemblies needed to meet the MPS. This ensures timely procurement and avoids material shortages.
- Capacity Requirements Planning (CRP): CRP assesses the production capacity required to fulfill the MPS. It considers factors such as machine availability, labor hours, and production processes. CRP helps identify potential capacity bottlenecks and allows for adjustments to the MPS or resource allocation.
- Shop Floor Control: This component monitors and tracks actual production progress against the planned schedule. Any deviations are promptly identified, allowing for corrective action to be taken.
Demand Forecasting in MRP II
The accuracy of demand forecasting directly influences the effectiveness of the entire MRP II system. Inaccurate forecasts can lead to excessive inventory, production delays, or material shortages. Therefore, sophisticated forecasting techniques are employed, often combining statistical methods with expert judgment and market analysis. Consider seasonal variations, economic trends, and promotional activities when developing forecasts.
Facets of Demand Forecasting:
- Qualitative Methods: Relying on expert opinions and market research for estimations.
- Quantitative Methods: Utilizing historical data and statistical techniques for prediction, like moving averages, exponential smoothing, and ARIMA models.
- Integration with CRM: Connecting the MRP II system with a customer relationship management (CRM) system for real-time sales data.
- Risk Assessment: Identifying and mitigating potential risks affecting demand accuracy.
- Continuous Improvement: Regularly reviewing and refining forecasting methods to improve accuracy over time.
Master Production Schedule (MPS) and its Role
The MPS is the cornerstone of MRP II. It represents a detailed, time-phased plan for producing finished goods. Its creation involves consolidating sales forecasts, considering available capacity, and resolving potential conflicts. The MPS must be realistic and achievable to avoid disrupting the entire production process. Effective MPS management requires collaboration between sales, production, and materials management departments.
Facets of MPS:
- Capacity Constraints: Understanding and incorporating production capacity limitations.
- Lead Times: Account for the time required for each stage of production.
- Inventory Levels: Optimizing inventory levels to minimize costs while ensuring sufficient stock.
- Order Prioritization: Establishing a system for prioritizing production orders based on urgency and importance.
- Periodic Review: Regularly reviewing and updating the MPS to reflect changes in demand or capacity.
Connecting the Dots: MRP and CRP
Materials Requirements Planning (MRP) and Capacity Requirements Planning (CRP) work in tandem within the MRP II system. MRP determines the materials needed based on the MPS, while CRP ensures sufficient capacity is available to produce those materials and finished goods. A crucial aspect of successful MRP II implementation lies in the seamless integration of MRP and CRP. Any discrepancies between material availability and production capacity need prompt resolution to maintain the system's integrity.
Further Analysis of MRP and CRP Integration:
MRP and CRP integration necessitates a system capable of processing vast amounts of data efficiently. This often requires the use of advanced software, capable of performing complex calculations and simulations. Furthermore, the accuracy of data input is critical for accurate planning, highlighting the need for real-time data capture and regular data validation. Any delays or inaccuracies in data transfer can undermine the entire system.
Real-World Example: A Furniture Manufacturer
Imagine a furniture manufacturer using MRP II to manage the production of custom-designed chairs. The sales forecast predicts a demand for 100 chairs in the next quarter, with specific orders specifying different wood types, fabric colors, and finishes. The MPS breaks down this demand into a weekly production schedule. MRP then calculates the quantities and delivery times for all raw materials, such as wood, fabric, and hardware, ensuring they arrive on time. CRP confirms the available machine capacity and skilled labor necessary to meet the production deadlines. This ensures timely completion of orders, optimal resource utilization, and satisfied customers.
FAQs on MRP II
Introduction: This section addresses common queries related to MRP II implementation and benefits.
Questions and Answers:
-
Q: What is the difference between MRP and MRP II? A: MRP focuses solely on materials planning, while MRP II incorporates all resources—materials, labor, and machinery.
-
Q: What software is needed for MRP II? A: Various ERP and MRP systems are available, ranging from standalone software to fully integrated enterprise-level solutions.
-
Q: How much does MRP II implementation cost? A: Costs vary greatly depending on the complexity of the manufacturing process, software choice, and consulting needs.
-
Q: What are the key challenges in implementing MRP II? A: Data accuracy, system complexity, resistance to change, and integration with existing systems.
-
Q: How can MRP II improve profitability? A: By reducing inventory costs, improving on-time delivery, and optimizing resource utilization.
-
Q: What are the long-term benefits of MRP II? A: Enhanced operational efficiency, improved decision-making, and increased competitiveness.
Summary of Key Takeaways:
This exploration of MRP II has highlighted its core components, implementation considerations, and significant benefits. Successful implementation requires careful planning, data accuracy, and ongoing system optimization.
Closing Message: In today's dynamic manufacturing landscape, robust planning systems are essential for survival and growth. MRP II, with its holistic approach to resource management, can empower manufacturers to achieve greater efficiency, profitability, and customer satisfaction. Embrace the potential of MRP II and unlock your manufacturing capabilities.
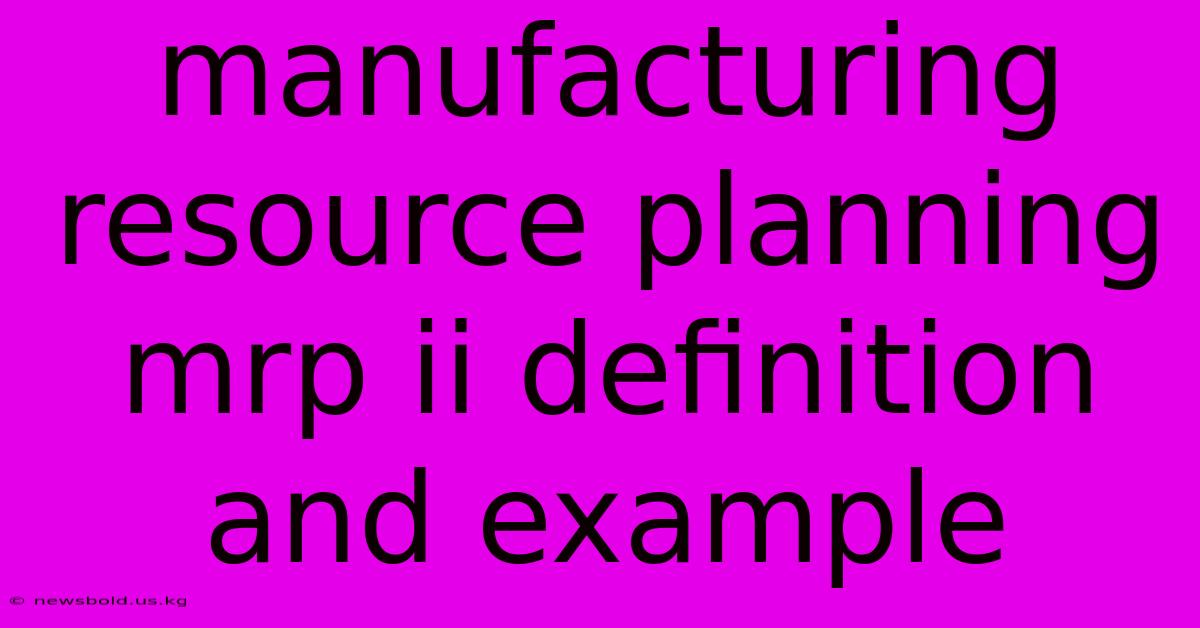
Thank you for taking the time to explore our website Manufacturing Resource Planning Mrp Ii Definition And Example. We hope you find the information useful. Feel free to contact us for any questions, and don’t forget to bookmark us for future visits!
We truly appreciate your visit to explore more about Manufacturing Resource Planning Mrp Ii Definition And Example. Let us know if you need further assistance. Be sure to bookmark this site and visit us again soon!
Featured Posts
-
Gibsons Paradox Definition
Jan 05, 2025
-
Foreign Currency Fx Swap Definition How It Works And Types
Jan 05, 2025
-
What Is Usda Funding Fee
Jan 05, 2025
-
Minimum Price Contract Definition
Jan 05, 2025
-
Hypothecation Definition And How It Works With Examples
Jan 05, 2025