Servicing Strip Definition
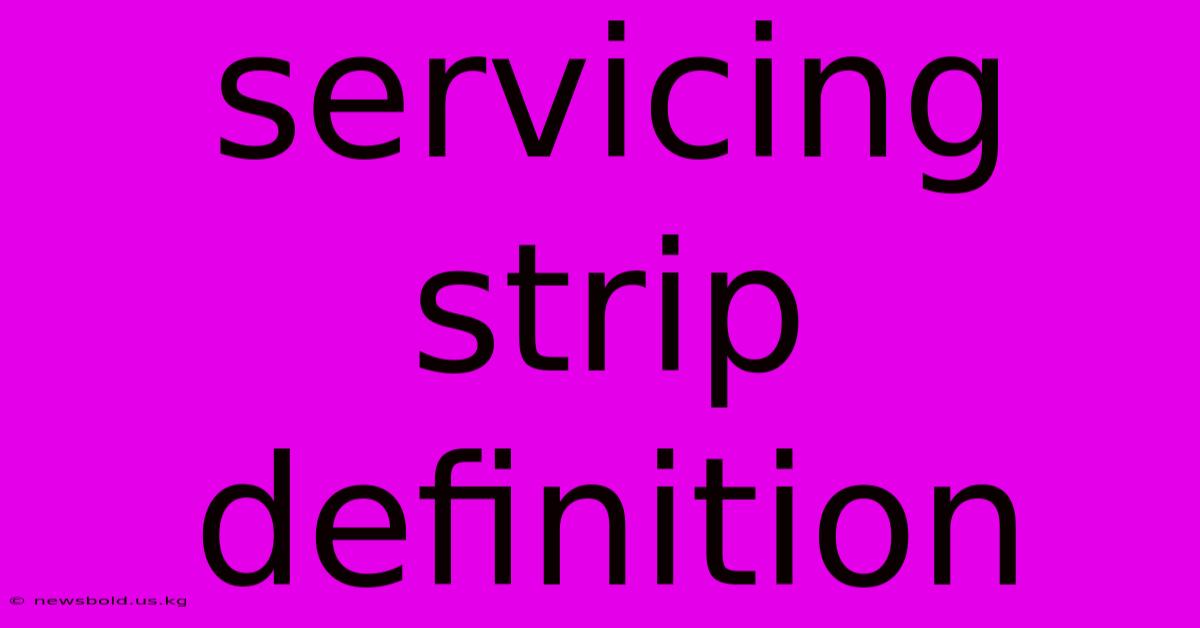
Discover more in-depth information on our site. Click the link below to dive deeper: Visit the Best Website meltwatermedia.ca. Make sure you don’t miss it!
Table of Contents
Unveiling the Mysteries of Strip Servicing: A Comprehensive Guide
Does the term "strip servicing" evoke images of complex machinery and intricate processes? It should! This often-overlooked aspect of industrial maintenance is crucial for efficient operation and longevity of equipment. This guide provides a comprehensive exploration of strip servicing, its importance, and key considerations for optimal implementation.
Editor's Note: This comprehensive guide to strip servicing was published today.
Why It Matters & Summary
Understanding strip servicing is essential for businesses relying on machinery with moving parts, particularly in manufacturing, processing, and automation. This article will delve into the definition, processes, and best practices associated with strip servicing, ultimately aiming to improve equipment uptime and reduce operational costs. Key terms explored include strip cleaning, lubrication, inspection, and preventative maintenance, all vital components of a robust strip servicing program.
Analysis
The information presented here is compiled from a thorough review of industry best practices, technical manuals, and expert opinions in mechanical engineering and maintenance. The goal is to deliver a practical and actionable guide applicable to diverse industries and equipment types.
Key Takeaways
Point | Description |
---|---|
Definition | The systematic process of cleaning, inspecting, lubricating, and repairing components within a strip. |
Importance | Ensures optimal equipment performance, extends lifespan, and minimizes downtime. |
Processes | Cleaning, inspection, lubrication, repair/replacement. |
Best Practices | Preventative maintenance scheduling, documented procedures, trained personnel. |
Cost-Effectiveness | Reduces repair costs and extends equipment life, leading to significant long-term savings. |
Let's move into a detailed exploration of strip servicing.
Strip Servicing: A Deep Dive
Introduction: This section will establish the foundational knowledge needed to understand strip servicing, examining its core components and their interdependencies.
Key Aspects:
- Strip Cleaning: Removing contaminants like dust, debris, and chemical residues.
- Strip Inspection: A thorough visual and sometimes instrumental examination for wear, tear, damage, or defects.
- Strip Lubrication: Applying appropriate lubricants to reduce friction and wear.
- Strip Repair/Replacement: Addressing damage or replacing worn-out components.
Discussion:
The four key aspects mentioned above are intrinsically linked. Effective cleaning allows for accurate inspection, which informs the necessary lubrication and repair decisions. Neglecting any one stage compromises the overall effectiveness of strip servicing.
Strip Cleaning
Introduction: Proper cleaning is the first step towards effective strip servicing, ensuring that all subsequent steps are accurate and effective.
Facets:
- Cleaning Methods: Manual cleaning, solvent cleaning, ultrasonic cleaning, etc. The choice depends on the strip material, the type of contamination, and the level of precision required.
- Cleaning Agents: Appropriate solvents and detergents should be used, always adhering to safety guidelines and environmental regulations. The wrong cleaning agent can damage the strip material.
- Safety Precautions: Personal protective equipment (PPE) like gloves, eye protection, and respiratory protection is mandatory during cleaning. Proper ventilation is also crucial, especially when using solvents.
- Documentation: A detailed record of the cleaning process, including the methods, agents, and any observed issues, should be maintained for traceability and future reference.
Summary: Thorough cleaning lays the groundwork for successful strip inspection and subsequent maintenance. The choice of cleaning methods and agents must align with the strip material and contaminants present.
Strip Inspection
Introduction: This stage involves a careful examination of the strip to identify potential issues and prevent catastrophic failures.
Facets:
- Visual Inspection: A thorough visual examination for signs of wear, cracks, corrosion, or damage. This is the first line of defense.
- Dimensional Inspection: Measuring the strip’s dimensions to ensure they are within the specified tolerances. Deviations can indicate wear or damage.
- Material Testing: Depending on the strip's material and application, further tests may be required to evaluate its integrity. Examples include hardness testing or microscopic examination.
- Documentation: All findings from the inspection, including photos and measurements, should be documented for record-keeping.
Summary: A comprehensive inspection helps prevent costly downtime by identifying and addressing potential problems before they escalate. Different inspection methods are used depending on the specific strip material and operational context.
Strip Lubrication
Introduction: Proper lubrication is vital for reducing friction, wear, and tear within the strip.
Facets:
- Lubricant Selection: Choosing the right lubricant is critical. Factors include the material of the strip, operating temperature, and the type of movement involved.
- Application Methods: Lubricants can be applied using various methods such as brushing, spraying, or automated lubrication systems. The best method depends on the accessibility and the desired level of precision.
- Lubrication Frequency: Regular lubrication is essential to maintain optimal performance. The frequency of lubrication depends on the operating conditions and the type of lubricant used.
- Over-lubrication Risks: Excessive lubrication can attract contaminants and lead to malfunctions. The correct amount of lubricant is crucial.
Summary: Correct lubrication is key to optimizing strip performance and extending its lifespan. Over-lubrication is just as damaging as insufficient lubrication.
Strip Repair and Replacement
Introduction: Addressing damage or replacing worn components is a crucial part of strip servicing.
Facets:
- Repair Methods: Techniques can range from simple repairs like welding or patching to more complex procedures. The choice depends on the extent of the damage.
- Component Replacement: Worn or damaged components should be replaced with high-quality equivalents. Using substandard parts can lead to premature failure.
- Quality Control: After repair or replacement, a thorough inspection is required to ensure the component functions correctly.
- Documentation: All repair and replacement work should be meticulously documented.
Summary: Timely repairs and replacements minimize costly breakdowns and improve overall equipment reliability. Maintaining a robust spare parts inventory is critical for efficient service.
FAQs about Strip Servicing
Introduction: This section answers frequently asked questions regarding strip servicing practices.
Questions:
-
Q: How often should strip servicing be performed? A: The frequency depends on factors like operating conditions, usage intensity, and the type of strip. A preventative maintenance schedule should be established.
-
Q: What are the consequences of neglecting strip servicing? A: Neglect can lead to premature wear, component failure, equipment downtime, and increased operational costs.
-
Q: What training is necessary for strip servicing? A: Personnel should be adequately trained in safe handling procedures, cleaning techniques, inspection methods, and repair protocols.
-
Q: What type of documentation is essential for strip servicing? A: Comprehensive records detailing cleaning, inspection, lubrication, repair, and replacement work, including dates, materials used, and observations.
-
Q: How can I choose the right lubricant for my strip? A: Consult the manufacturer's recommendations or an experienced lubrication specialist. Consider operating conditions and strip material.
-
Q: What are the safety precautions to be followed during strip servicing? A: Appropriate PPE, proper ventilation, adherence to safety regulations, and awareness of potential hazards (e.g., solvents, moving parts).
Summary: Regular and properly documented strip servicing is key to maintaining equipment efficiency and preventing costly failures.
Tips for Effective Strip Servicing
Introduction: This section provides practical tips for implementing a successful strip servicing program.
Tips:
- Develop a Preventative Maintenance Schedule: Establish a regular schedule based on usage and operational conditions.
- Use High-Quality Lubricants and Cleaning Agents: Invest in top-tier products to maximize performance and minimize damage.
- Train Personnel Properly: Ensure technicians are adequately trained and knowledgeable in all aspects of strip servicing.
- Document Everything: Maintain detailed records of all servicing activities for future reference and analysis.
- Regularly Inspect Equipment: Perform routine visual inspections to identify potential issues early.
- Implement a Spare Parts Inventory System: Maintain a sufficient stock of replacement parts to minimize downtime.
- Utilize Advanced Technology: Consider using automated lubrication systems or advanced inspection tools to enhance efficiency and accuracy.
Summary: A well-planned and executed strip servicing program is essential for optimal equipment performance and long-term cost savings.
Summary of Strip Servicing Exploration
This article has provided a comprehensive overview of strip servicing, highlighting its crucial role in maintaining industrial machinery. The processes involved – cleaning, inspection, lubrication, and repair/replacement – were explored in detail, emphasizing their interdependencies and importance in preventing equipment failure and maximizing operational efficiency.
Closing Message: Implementing a robust strip servicing program is not merely a matter of maintenance; it's a strategic investment that contributes directly to increased productivity, reduced costs, and improved overall operational reliability. Prioritize strip servicing as a cornerstone of your preventative maintenance strategy.
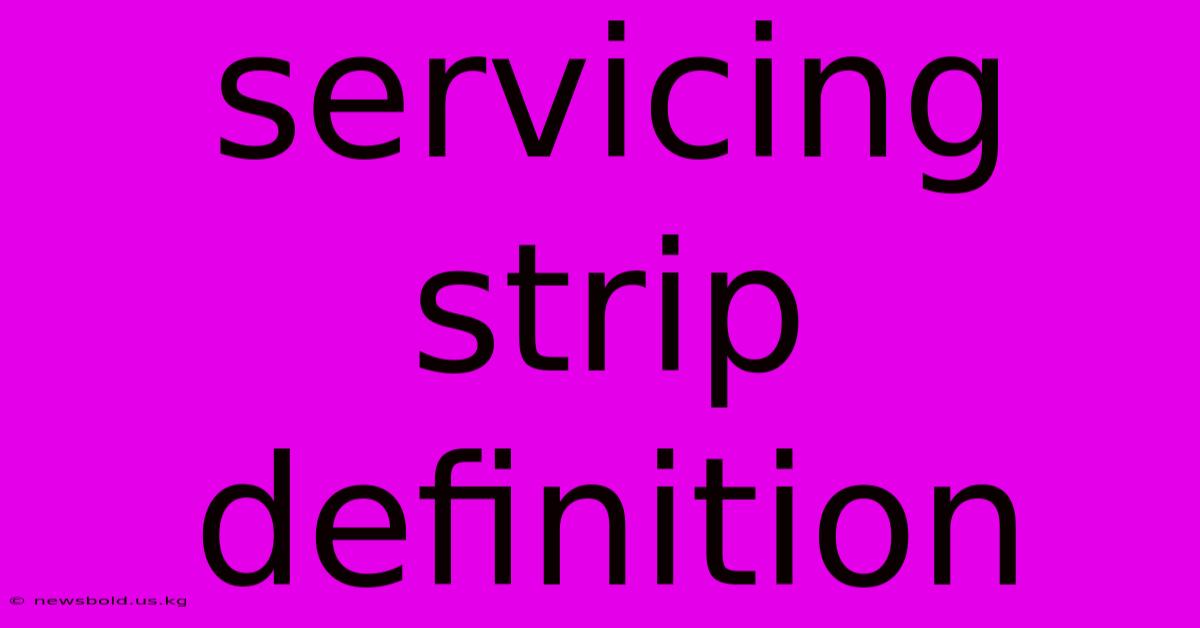
Thank you for taking the time to explore our website Servicing Strip Definition. We hope you find the information useful. Feel free to contact us for any questions, and don’t forget to bookmark us for future visits!
We truly appreciate your visit to explore more about Servicing Strip Definition. Let us know if you need further assistance. Be sure to bookmark this site and visit us again soon!
Featured Posts
-
Strong Hands Definition
Jan 08, 2025
-
What Is Bottom Up Budgeting
Jan 08, 2025
-
Successive Periods Definition
Jan 08, 2025
-
Terminal Capitalization Rate Definition And Calculation Example
Jan 08, 2025
-
Variable Ratio Write Definition
Jan 08, 2025