What Are Holding Costs Definition How They Work And Example
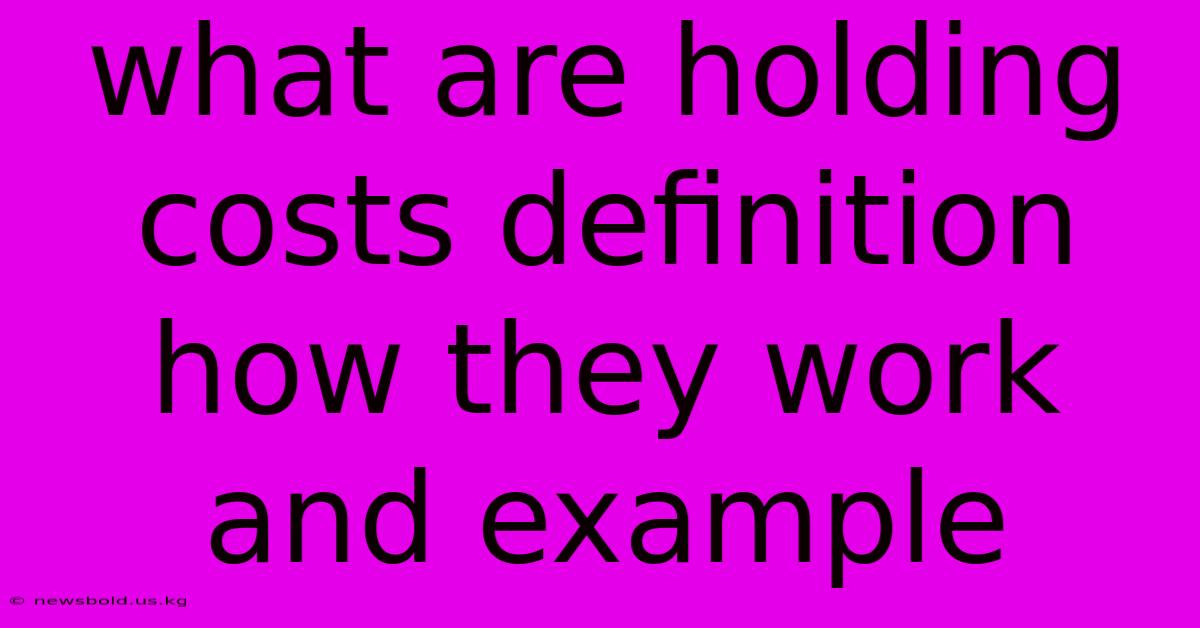
Discover more in-depth information on our site. Click the link below to dive deeper: Visit the Best Website meltwatermedia.ca. Make sure you don’t miss it!
Table of Contents
Unveiling Holding Costs: A Deep Dive into Inventory Management
What are holding costs, and why should businesses care? The answer is simple: they represent a significant, often overlooked, drain on profitability. Understanding and minimizing holding costs is crucial for maintaining a healthy bottom line. This comprehensive guide explores the definition, mechanics, and practical examples of holding costs, empowering businesses to make informed decisions.
Editor's Note: This in-depth analysis of holding costs has been published today to provide businesses with practical strategies for optimizing inventory management.
Why It Matters & Summary
Holding costs, also known as carrying costs or inventory holding costs, encompass all expenses associated with storing and maintaining inventory until it's sold. These costs directly impact profitability, making their understanding vital for effective inventory management. This article provides a thorough examination of holding costs, including their components, calculation methods, and strategies for minimization. Relevant semantic keywords include inventory management, warehousing costs, storage costs, obsolescence, insurance, capital costs, and carrying costs.
Analysis
This analysis leverages a combination of industry research, case studies, and practical examples to provide a comprehensive guide to holding costs. Data from various sources, including industry reports and financial statements of publicly traded companies, were analyzed to identify common cost components and their impact on profitability. The information presented aims to help businesses of all sizes better understand and manage their inventory holding costs.
Key Takeaways
Aspect | Description |
---|---|
Definition | Total cost of storing and maintaining unsold inventory. |
Components | Storage, insurance, taxes, obsolescence, capital costs, and opportunity costs. |
Calculation | Varies depending on the business and inventory type; often expressed as a percentage of inventory value. |
Minimization Strategies | Efficient warehousing, improved forecasting, optimized ordering, and inventory control systems. |
Impact | Directly impacts profitability; high holding costs reduce profit margins. |
Let's transition into a deeper exploration of this critical aspect of business operations.
Holding Costs: A Comprehensive Overview
Holding costs encompass all expenses incurred from the moment inventory enters a warehouse until it’s sold. These costs are not merely about physical storage; they represent a broader financial burden.
Key Aspects of Holding Costs
- Storage Costs: Rent, utilities (electricity, heating, cooling), and maintenance of warehouse facilities. This is often the most significant component.
- Insurance Costs: Premiums paid to insure inventory against damage, loss, or theft.
- Taxes: Property taxes on inventory held in a warehouse.
- Obsolescence Costs: The loss in value of inventory due to technological advancements, changes in consumer demand, or expiration dates (especially relevant for perishable goods). This is often the most unpredictable component.
- Capital Costs: The opportunity cost of the capital tied up in inventory. This money could be used for other investments, generating a return. This is a critical but often overlooked factor.
- Handling Costs: Labor costs associated with moving, receiving, and managing inventory within the warehouse.
- Shrinkage Costs: Losses due to theft, damage, or spoilage.
Discussion: Unpacking the Significance of Each Component
The connection between each cost component and the overall impact on profitability is undeniable. High storage costs, for instance, directly translate to reduced profit margins. Obsolescence, on the other hand, presents a significant risk, especially in industries with rapid technological advancements. Let's examine the interplay of these components in more detail.
Storage Costs
Storage costs are directly tied to warehouse size, location, and the efficiency of the warehouse management system. A poorly organized warehouse can significantly increase handling time, leading to increased labor costs and potentially higher damage rates.
Obsolescence Costs
The risk of obsolescence is particularly high for technology products, fashion items, and seasonal goods. Accurate demand forecasting and efficient inventory turnover are crucial for minimizing this cost. A detailed analysis of sales trends and market research is necessary to predict potential obsolescence.
Capital Costs
Capital tied up in inventory represents a significant opportunity cost. The money invested in inventory could have been used for more profitable ventures, such as research and development, marketing campaigns, or debt reduction. This hidden cost significantly impacts the overall return on investment.
Analyzing Holding Cost Components
This section delves deeper into the analysis of each key component, emphasizing its facets, examples, and potential mitigations.
Storage Costs
Facets:
- Role: Housing and protecting inventory.
- Examples: Rent, utilities, security systems, shelving.
- Risks & Mitigations: High rent in prime locations; mitigation: consider alternative locations, optimize warehouse layout.
- Impacts & Implications: Direct impact on profitability; increased costs reduce profit margins.
Obsolescence Costs
Facets:
- Role: Loss in inventory value due to age or changes in market demand.
- Examples: Outdated technology, seasonal items remaining unsold.
- Risks & Mitigations: Poor demand forecasting, long lead times; mitigation: robust forecasting, agile inventory management.
- Impacts & Implications: Significant financial losses, reduced profitability, potential write-offs.
Capital Costs
Facets:
- Role: Opportunity cost of capital tied up in inventory.
- Examples: Funds that could have earned interest, been invested elsewhere.
- Risks & Mitigations: High inventory levels; mitigation: Just-in-time inventory systems, efficient supply chain.
- Impacts & Implications: Reduced return on investment, hindering business growth.
Calculating Holding Costs
There's no single formula; the calculation depends on the specific components and the business's accounting practices. A common approach expresses holding costs as a percentage of the average inventory value. This percentage typically ranges from 15% to 30%, depending on the industry and inventory characteristics. A more detailed breakdown involves calculating the cost of each component and summing them up.
Minimizing Holding Costs: Proven Strategies
Several strategies can help businesses reduce holding costs significantly. These include:
- Improve demand forecasting: Accurate demand prediction helps optimize inventory levels.
- Implement a Just-in-Time (JIT) inventory system: This system minimizes inventory holding by receiving goods only as needed.
- Optimize warehouse layout and operations: Efficient warehouse organization reduces handling costs and improves space utilization.
- Negotiate better terms with suppliers: Secure discounts or favorable payment terms to reduce overall costs.
- Regularly review and adjust inventory levels: Monitor stock levels and make necessary adjustments to prevent overstocking.
- Invest in inventory management software: These systems provide real-time visibility into inventory levels, enabling better decision-making.
- Consider alternative storage solutions: Explore options like cloud warehousing or third-party logistics (3PL) providers to reduce fixed storage costs.
FAQs on Holding Costs
Introduction: This section addresses common questions regarding holding costs.
Questions & Answers:
- Q: How are holding costs different from order costs? A: Holding costs are related to storing inventory, while order costs are associated with placing and receiving orders.
- Q: What is the typical holding cost percentage? A: It typically ranges from 15% to 30% of average inventory value but varies significantly by industry.
- Q: How can I accurately calculate my holding costs? A: Break down costs into individual components (storage, insurance, taxes, etc.) and sum them up.
- Q: What is the impact of high holding costs? A: Reduced profitability, decreased return on investment, and potential cash flow issues.
- Q: Are there any software solutions to help manage holding costs? A: Yes, many inventory management software programs offer features to track and analyze holding costs.
- Q: How can I reduce obsolescence costs? A: Implement effective demand forecasting, use shorter lead times, and consider strategies like product lifecycle management.
Summary: Understanding and minimizing holding costs is crucial for financial health.
Tips for Effective Holding Cost Management
Introduction: This section offers actionable tips for optimizing inventory management and reducing holding costs.
Tips:
- Regular inventory audits: Conduct regular stock checks to identify slow-moving items or potential obsolescence.
- Negotiate favorable shipping rates: Lower transportation costs can significantly reduce overall inventory expenses.
- Implement barcode or RFID tracking: Accurate tracking improves inventory accuracy and reduces shrinkage.
- Train staff in proper inventory handling: Proper handling minimizes damages and spoilage.
- Consider using a 3PL provider: Outsourcing warehousing and logistics can reduce operational costs.
- Develop a robust inventory control system: A well-structured system improves accuracy and minimizes waste.
Summary: Proactive inventory management is key to minimizing holding costs and maximizing profitability.
Summary of Holding Cost Analysis
This analysis explored the multifaceted nature of holding costs, emphasizing their significance in overall business profitability. Understanding and effectively managing these costs is crucial for efficient inventory control and sustainable growth.
Closing Message: By implementing the strategies and insights shared in this guide, businesses can achieve a significant reduction in holding costs, ultimately boosting profitability and competitive advantage. Proactive management of inventory, coupled with data-driven decision-making, will pave the way for a more efficient and profitable future.
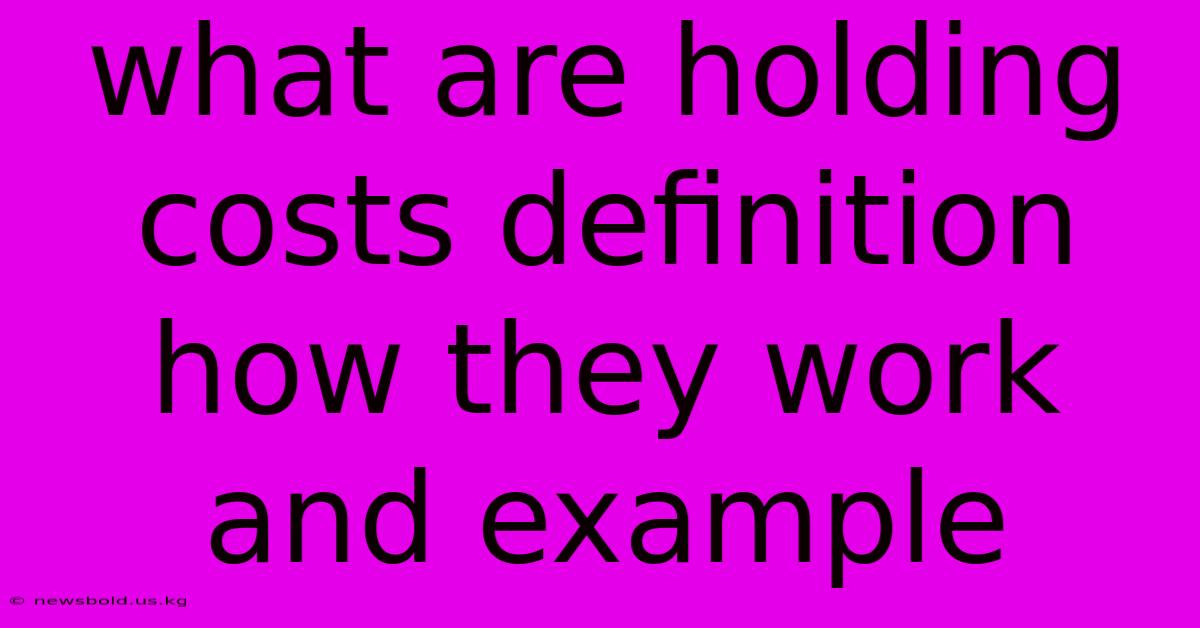
Thank you for taking the time to explore our website What Are Holding Costs Definition How They Work And Example. We hope you find the information useful. Feel free to contact us for any questions, and don’t forget to bookmark us for future visits!
We truly appreciate your visit to explore more about What Are Holding Costs Definition How They Work And Example. Let us know if you need further assistance. Be sure to bookmark this site and visit us again soon!
Featured Posts
-
Institute For Divorce Financial Analysts Idfa Definition
Jan 05, 2025
-
General Motors Indicator Definition
Jan 05, 2025
-
What Is Ho 2 Insurance
Jan 05, 2025
-
Where To Find Debt On Financial Statements
Jan 05, 2025
-
Government Sponsored Retirement Arrangement Gsra Definition
Jan 05, 2025