What Is Gearing Definition Hows Its Measured And Example
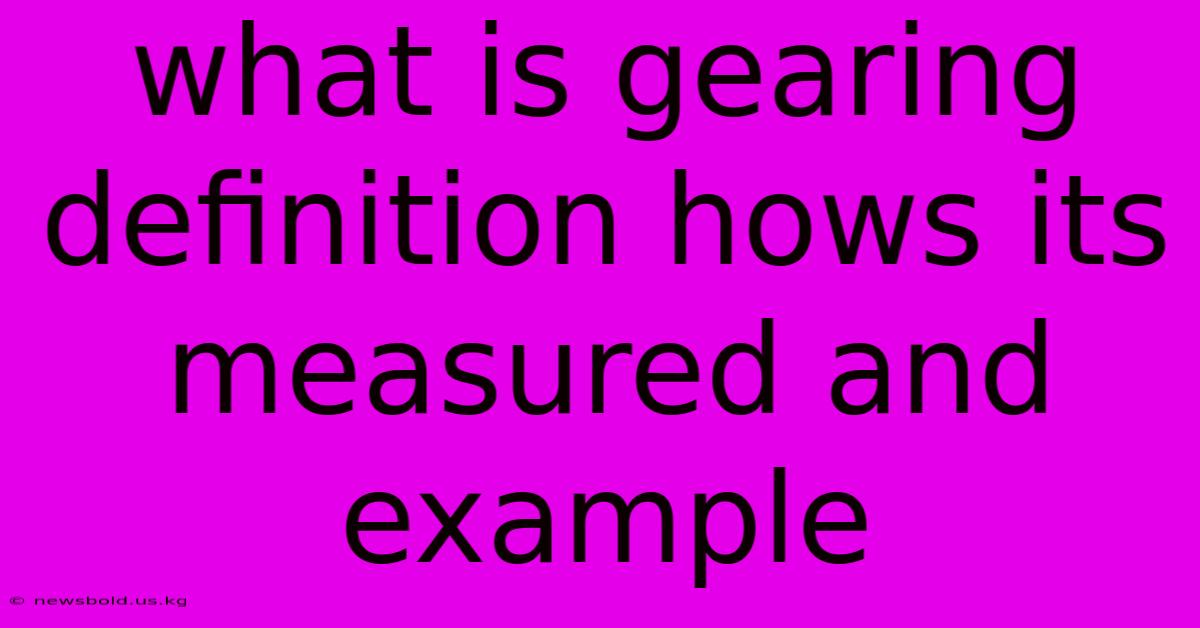
Discover more in-depth information on our site. Click the link below to dive deeper: Visit the Best Website meltwatermedia.ca. Make sure you don’t miss it!
Table of Contents
Unlocking the Power of Gearing: Definition, Measurement, and Real-World Examples
What precisely determines a machine's ability to amplify force or speed? The answer lies in the fascinating world of gearing. This article delves into the definition of gearing, exploring its measurement and illustrating its applications with practical examples.
Editor's Note: This comprehensive guide to gearing has been published today, providing readers with a clear understanding of this critical mechanical principle.
Why It Matters & Summary
Understanding gearing is fundamental across numerous engineering disciplines. From automobiles and bicycles to industrial machinery and robotic systems, gearing systems are ubiquitous, enabling efficient power transmission and mechanical advantage. This article summarizes the core concepts of gearing, including gear ratios, types of gears, and methods for calculating gear ratios, offering a practical guide for both students and professionals. Key semantic keywords include gear ratio, gear teeth, torque, speed, mechanical advantage, and various gear types (spur, helical, bevel, worm).
Analysis
The information presented in this article is compiled from widely accepted engineering principles and textbooks on mechanics and machine design. The analysis emphasizes clarity and accessibility, avoiding overly technical jargon while maintaining scientific accuracy. The examples chosen represent common applications of gearing to enhance comprehension.
Key Takeaways
Feature | Description |
---|---|
Gearing Definition | The mechanism using gears to transmit rotational motion and torque. |
Gear Ratio | The ratio of the number of teeth on the driven gear to the number of teeth on the driving gear. |
Measurement | Calculated from the number of teeth or diameters of the gears involved. |
Mechanical Advantage | The ratio of output torque to input torque, often amplified by gearing. |
Applications | Found in numerous machines, from bicycles to industrial equipment. |
Let's now delve into the intricacies of gearing.
Gearing: A Deep Dive
Gearing, at its core, is a mechanism employing toothed wheels, known as gears, to transmit rotational motion and torque from one shaft to another. This transmission can alter the speed and torque, providing mechanical advantage, depending on the gear arrangement. The effectiveness of the gearing system is primarily determined by the gear ratio.
Key Aspects of Gearing
-
Gear Ratio: This is the fundamental parameter of a gearing system. It's the ratio of the output speed (or torque) to the input speed (or torque). A gear ratio greater than 1 implies a reduction in speed but an increase in torque, while a ratio less than 1 signifies an increase in speed with a reduction in torque.
-
Gear Types: Various gear types exist, each suited for specific applications. Common types include spur gears (parallel shafts), helical gears (parallel shafts, smoother operation), bevel gears (intersecting shafts), and worm gears (non-parallel, high torque ratios).
-
Gear Teeth: The design of gear teeth is crucial for efficient and smooth power transmission. Proper tooth profile, pressure angle, and module (a measure of tooth size) are key considerations in gear design to minimize wear and noise.
Exploring Gear Ratio Calculations
The gear ratio can be calculated in several ways, all ultimately yielding the same result.
-
Using Number of Teeth: The simplest method involves the number of teeth on each gear. If N<sub>1</sub> represents the number of teeth on the driving gear and N<sub>2</sub> represents the number of teeth on the driven gear, the gear ratio (GR) is:
GR = N<sub>2</sub> / N<sub>1</sub>
-
Using Gear Diameters: Alternatively, if the diameters (D<sub>1</sub> and D<sub>2</sub>) of the gears are known, the gear ratio can be computed as:
GR = D<sub>2</sub> / D<sub>1</sub>
This equivalence holds true assuming the gears have the same module (tooth size).
Practical Applications of Gearing: Real-World Examples
The applications of gearing span numerous industries and technologies. Let's examine a few prominent examples:
1. Bicycle Transmission
A bicycle's gear system is a prime example of gearing's ability to alter speed and torque. Smaller gears in front (driving gear) and larger gears in the rear (driven gear) provide a lower gear ratio, allowing for easier pedaling uphill at the cost of speed. Conversely, larger front gears and smaller rear gears provide a higher gear ratio, enabling faster speeds on level terrain but requiring more effort.
2. Automobile Transmission
Automotive transmissions use a series of gears to adapt the engine's speed and torque to various driving conditions. Lower gears provide higher torque for acceleration and hill climbing, while higher gears allow for higher speeds at lower engine RPMs for fuel efficiency.
3. Industrial Machinery
Gearing plays a vital role in numerous industrial machines. In a reduction gearbox, for instance, a large gear driven by a smaller gear drastically reduces the speed of a motor while significantly increasing its torque, making it suitable for heavy-duty tasks like lifting or material handling.
4. Clockwork Mechanisms
Clocks and watches employ intricate gear trains to accurately measure and display time. The carefully chosen gear ratios ensure precise movements of the hands based on the consistent rotation of the mainspring.
Specific Points within Gearing Systems
Gear Tooth Design and Wear
The design of gear teeth significantly impacts the efficiency and longevity of the gearing system. Factors such as tooth profile (involute is common), pressure angle, and module must be carefully chosen to ensure proper meshing and minimize wear and tear. Incorrect tooth design can lead to increased noise, vibration, and premature failure.
Facets:
- Role: To ensure smooth, efficient transmission of power.
- Examples: Involute profile, different pressure angles, various modules.
- Risks and Mitigations: Incorrect design leads to noise, vibration, and wear; proper design and material selection mitigate these.
- Impacts and Implications: Affects efficiency, lifespan, noise level, and overall system performance.
The connection between gear tooth design and the overall performance of the gearing system is direct and significant. Optimized tooth design is essential for efficiency, longevity, and reduced noise and vibration.
Gear Ratio and Mechanical Advantage
The gear ratio is directly related to the mechanical advantage offered by the gearing system. Mechanical advantage refers to the amplification of force or torque. A higher gear ratio translates to a greater mechanical advantage, meaning the output torque is significantly larger than the input torque. This is crucial in applications where high torque is needed, even at the cost of reduced speed.
Further Analysis:
Consider a gear reduction system with a gear ratio of 10:1. This means the output shaft rotates 10 times slower than the input shaft, but the output torque is 10 times greater. This principle finds wide application in heavy-duty machinery and power tools.
Closing:
Optimizing the gear ratio is essential for maximizing the efficiency and effectiveness of the gearing system, tailoring it to the specific requirements of the application.
FAQ
Introduction:
This section addresses frequently asked questions about gearing systems.
Questions:
-
Q: What is backlash in gearing? A: Backlash is the clearance between meshing gear teeth. While some backlash is necessary for lubrication, excessive backlash can lead to noise and inefficiency.
-
Q: How does lubrication affect gearing? A: Lubrication is critical for reducing friction, wear, and noise in gearing systems. Proper lubrication extends the lifespan of the gears and improves efficiency.
-
Q: What are the different materials used in gear manufacturing? A: Various materials, including steel, cast iron, plastics, and composites, are used depending on the application's requirements for strength, wear resistance, and cost.
-
Q: How is gear noise minimized? A: Gear noise can be minimized through proper gear design, accurate manufacturing, precise alignment, and effective lubrication.
-
Q: What is the difference between a simple gear train and a compound gear train? A: A simple gear train involves two gears, while a compound gear train consists of multiple gears on multiple shafts.
-
Q: How is the efficiency of a gearing system measured? A: Gearing system efficiency is the ratio of output power to input power. Losses due to friction and other factors reduce overall efficiency.
Summary:
Understanding the different aspects of gearing is key to selecting and designing efficient and effective systems.
Tips for Effective Gearing System Design
Introduction:
This section offers practical tips for optimizing the design and maintenance of gearing systems.
Tips:
-
Proper Gear Selection: Carefully select gear types and materials based on the specific application's requirements for load, speed, and environment.
-
Precise Alignment: Ensure accurate alignment of gears to minimize wear and noise. Misalignment can lead to rapid gear failure.
-
Adequate Lubrication: Employ appropriate lubricants and lubrication schedules to reduce friction, wear, and noise.
-
Regular Inspection and Maintenance: Regularly inspect gears for wear, damage, and misalignment. Implement preventive maintenance to extend their lifespan.
-
Accurate Gear Ratio Calculation: Accurately calculate gear ratios to achieve the desired speed and torque outputs.
-
Consider Thermal Effects: Account for thermal effects due to friction during gear design, ensuring adequate cooling to prevent overheating and damage.
-
Noise Reduction Techniques: Implement design and operational strategies to minimize gear noise, including proper lubrication, accurate alignment, and optimized tooth profiles.
-
Material Selection: Select materials with appropriate strength, hardness, and wear resistance based on the anticipated load and operating conditions.
Summary:
Following these tips can significantly enhance the performance, reliability, and lifespan of any gearing system.
Summary of Gearing
This article has explored the fundamental aspects of gearing, encompassing its definition, measurement, various types, and real-world applications. Understanding the gear ratio, tooth design, and material selection is crucial for optimizing power transmission and achieving the desired mechanical advantage.
Closing Message
Gearing, a seemingly simple concept, underlies the functionality of countless machines. Its profound impact on engineering and technology should not be underestimated. By understanding and implementing the principles discussed here, engineers and designers can create more efficient, reliable, and effective mechanical systems. Further exploration into the specialized aspects of gear design will inevitably lead to even more innovative solutions for future technological advancements.
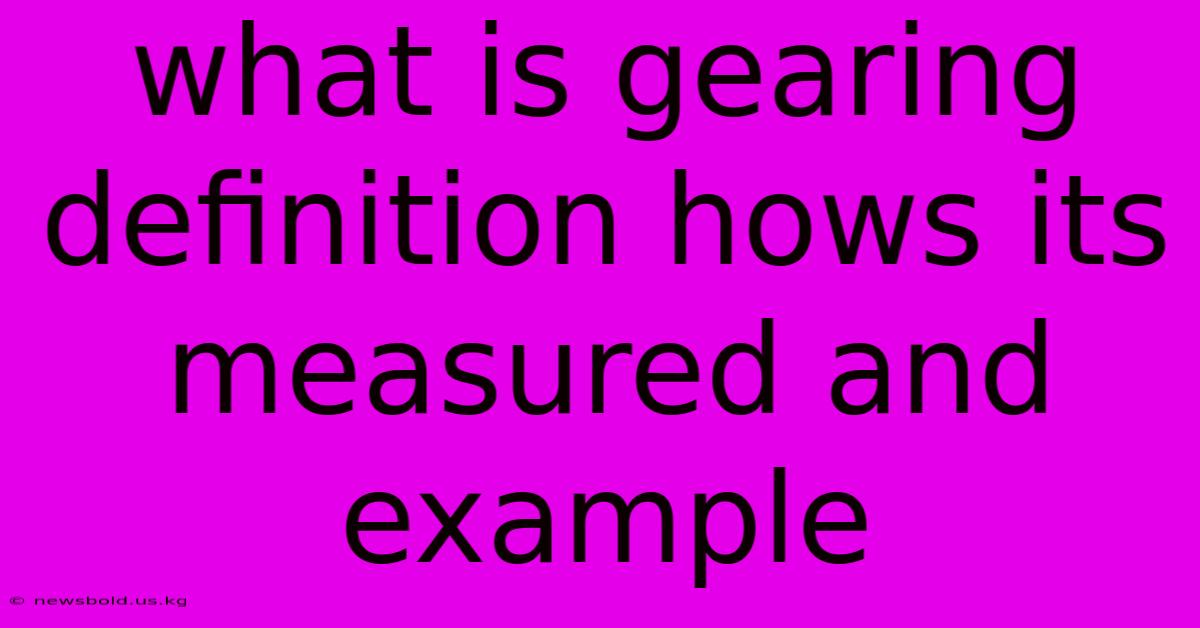
Thank you for taking the time to explore our website What Is Gearing Definition Hows Its Measured And Example. We hope you find the information useful. Feel free to contact us for any questions, and don’t forget to bookmark us for future visits!
We truly appreciate your visit to explore more about What Is Gearing Definition Hows Its Measured And Example. Let us know if you need further assistance. Be sure to bookmark this site and visit us again soon!
Featured Posts
-
What Is A Hardship Withdrawal Definition Rules And Alternatives
Jan 05, 2025
-
Intercompany Products Suits Exclusion Definition
Jan 05, 2025
-
Infrastructure Trust Definition
Jan 05, 2025
-
Hammering Definition
Jan 05, 2025
-
Index Etf Definition Types Advantages And Risks
Jan 05, 2025