What Is Purchase Order Lead Time Definition And How It Works
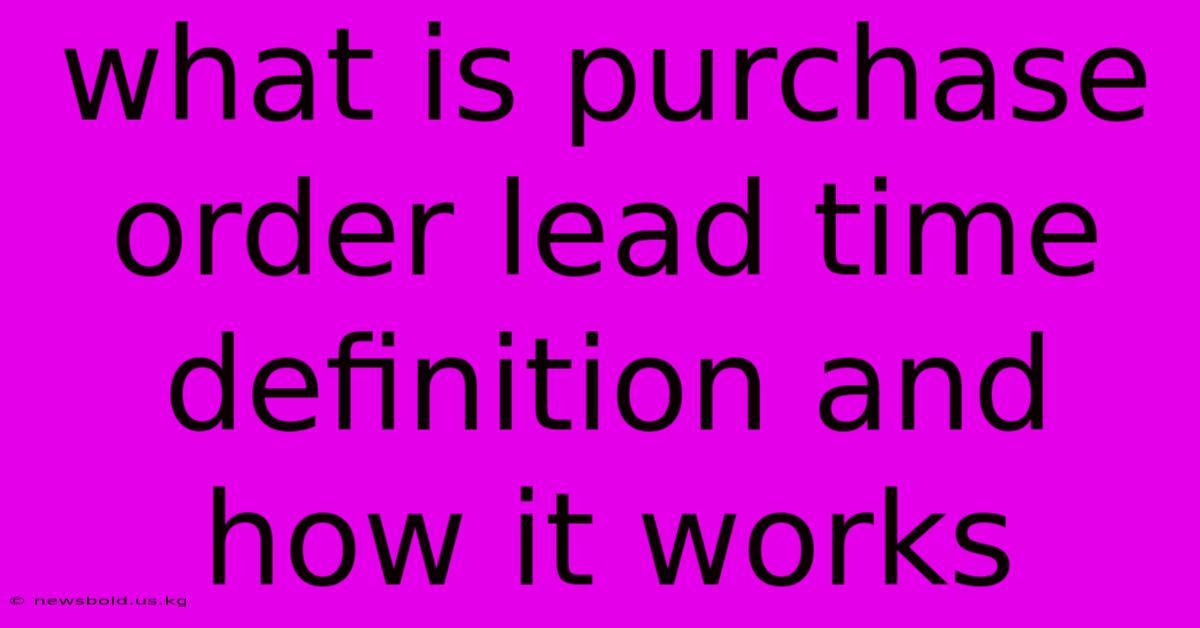
Discover more in-depth information on our site. Click the link below to dive deeper: Visit the Best Website meltwatermedia.ca. Make sure you don’t miss it!
Table of Contents
Unveiling Purchase Order Lead Time: A Comprehensive Guide
What precisely defines purchase order lead time, and how does this crucial metric function within a business context? Understanding purchase order lead time is paramount for efficient supply chain management. Its impact on inventory levels, production schedules, and ultimately, customer satisfaction, cannot be overstated. This comprehensive guide explores purchase order lead time, offering insights and practical applications.
Editor's Note: This guide to understanding purchase order lead time was published today to provide businesses with the knowledge to optimize their procurement processes.
Why It Matters & Summary
Purchase order lead time (POLT) is a critical metric impacting operational efficiency and profitability. This guide provides a detailed explanation of POLT, including its calculation, factors influencing it, and strategies for optimization. The discussion covers key aspects such as order placement, vendor processing, production time, shipping, and receiving, highlighting their individual and collective influence on the overall lead time. Understanding and managing POLT is crucial for inventory control, meeting customer demand, and maintaining a competitive edge. Relevant semantic keywords include: procurement, supply chain, inventory management, order fulfillment, vendor management, production planning, delivery time, and operational efficiency.
Analysis
The information presented in this guide is based on established supply chain management principles and best practices. Analysis draws from extensive research across various industries, encompassing case studies, industry reports, and academic publications focused on procurement and operational efficiency. The aim is to provide a practical and actionable understanding of POLT for businesses of all sizes, equipping them to make informed decisions regarding their procurement and inventory management strategies.
Key Takeaways
Key Aspect | Description |
---|---|
Purchase Order Lead Time (POLT) | The total time elapsed between placing a purchase order and receiving the goods or services. |
Order Placement | Time taken to initiate and submit the purchase order. |
Vendor Processing | Time taken by the vendor to process the order, including order confirmation and scheduling production. |
Production Time | Time taken to manufacture or produce the goods ordered. |
Shipping Time | Time taken to transport the goods from the vendor to the buyer. |
Receiving Time | Time taken to receive and inspect the goods upon arrival. |
POLT Optimization | Strategies to shorten lead times, including vendor selection, inventory management, and communication. |
Purchase Order Lead Time: A Detailed Exploration
Introduction: This section delves into the core components of purchase order lead time, examining each stage in the process and identifying potential bottlenecks. Understanding each stage is fundamental to effectively managing and optimizing POLT.
Key Aspects:
- Order Placement: This encompasses internal processes, such as requisition creation, purchase order generation, and approval workflows. Efficiency here is crucial for initiating the entire process promptly.
- Vendor Processing: This phase includes order acknowledgment, scheduling production, and quality control checks at the vendor's facility. The vendor's internal processes significantly impact this stage.
- Production Time: The time it takes to manufacture the goods depends heavily on the complexity of the product, manufacturing capacity, and availability of raw materials. This is often the longest phase in the POLT.
- Shipping Time: This encompasses packaging, transportation mode selection (e.g., air freight, sea freight, trucking), and transit time. Distance, logistics, and transportation infrastructure all influence shipping time.
- Receiving Time: This final phase involves unloading, inspection for damages or discrepancies, and documentation processing. Efficient receiving procedures are essential for minimizing delays.
Order Placement: Streamlining the Initial Stages
Introduction: The efficiency of the order placement phase significantly impacts the overall POLT. Streamlining this process is vital for reducing lead times and improving operational efficiency.
Facets:
- Role of Procurement Systems: Automated purchase order systems can significantly reduce the time required to generate and approve purchase orders, minimizing manual errors and delays.
- Example of Efficient Processes: Implementing electronic purchase order systems with automated approvals can substantially reduce order placement time.
- Risks and Mitigations: Inefficient requisition processes or lengthy approval workflows can delay order placement, necessitating improved workflows and authorization processes.
- Impacts and Implications: Delays in order placement have a ripple effect, extending the overall lead time and potentially impacting production schedules.
Vendor Processing: Optimizing Supplier Relationships
Introduction: The vendor's internal processes represent a crucial element of POLT. Establishing strong supplier relationships and collaborative processes is essential to optimize this phase.
Facets:
- Collaborative Vendor Relationships: Open communication and information sharing between buyer and supplier can help resolve issues proactively, reducing processing delays.
- Example of Effective Collaboration: Regularly scheduled meetings with key suppliers to discuss order fulfillment and potential challenges can mitigate delays.
- Risks and Mitigations: Lack of communication or unforeseen supplier issues can disrupt vendor processing, necessitating robust contingency plans and communication protocols.
- Impacts and Implications: Supplier inefficiencies can significantly impact the overall POLT, potentially leading to production delays and stockouts.
Production Time: Managing Manufacturing Processes
Introduction: Production time often constitutes the largest portion of POLT. This section analyzes strategies to optimize manufacturing processes and minimize production lead times.
Further Analysis: Lean manufacturing principles, such as Just-in-Time (JIT) inventory management and continuous improvement (Kaizen), can significantly reduce production lead times. Effective capacity planning, efficient scheduling, and proactive maintenance can also improve production efficiency.
Closing: Optimizing production time requires a multifaceted approach encompassing process improvements, technology adoption, and strategic supplier relationships.
Shipping Time: Expediting Delivery
Introduction: Shipping time is influenced by the chosen mode of transportation, distance, and logistical efficiency. This section examines how to optimize shipping processes for quicker delivery.
Information Table:
Transportation Mode | Speed | Cost | Reliability | Suitability |
---|---|---|---|---|
Air Freight | Very Fast | High | High | Urgent shipments, valuable goods |
Sea Freight | Slow | Low | Moderate | Large shipments, less time-sensitive goods |
Trucking | Moderate | Moderate | Moderate | Regional shipments, flexible delivery |
Receiving Time: Ensuring Efficient Goods Handling
Introduction: The final stage of POLT, receiving, involves handling the goods upon arrival. Efficient receiving processes are crucial for minimizing delays and ensuring accurate inventory updates.
Further Analysis: Implementing barcode scanning, RFID tracking, and automated receiving systems can improve efficiency. Thorough inspection upon arrival helps ensure goods meet quality standards and specifications.
Closing: A well-organized receiving department is pivotal for accurate inventory control and timely order completion.
FAQ
Introduction: This section addresses frequently asked questions about purchase order lead time.
Questions:
- Q: What are the key factors that influence purchase order lead time? A: Order placement, vendor processing, production time, shipping time, and receiving time all influence POLT.
- Q: How can businesses reduce their purchase order lead times? A: Streamlining processes, improving communication, optimizing vendor relationships, and adopting technology can reduce POLT.
- Q: What is the importance of monitoring purchase order lead time? A: Monitoring POLT allows businesses to identify bottlenecks, optimize processes, and improve efficiency.
- Q: How can businesses measure their purchase order lead time? A: Tracking the time elapsed from order placement to goods receipt provides a precise measurement.
- Q: What are the consequences of long purchase order lead times? A: Long POLTs can lead to stockouts, production delays, increased inventory costs, and dissatisfied customers.
- Q: How can I integrate POLT data into broader supply chain management strategies? A: Integrate POLT data into demand forecasting, production planning, and inventory management systems for comprehensive supply chain optimization.
Summary: Understanding and managing purchase order lead time is crucial for efficient supply chain management. Optimizing each stage of the process—from order placement to receiving—is essential for minimizing lead times and improving operational efficiency.
Closing Message: By proactively addressing the factors influencing POLT and implementing effective strategies, businesses can enhance their competitiveness, improve customer satisfaction, and boost overall profitability. Continuous monitoring and improvement of POLT remain vital for ongoing success.
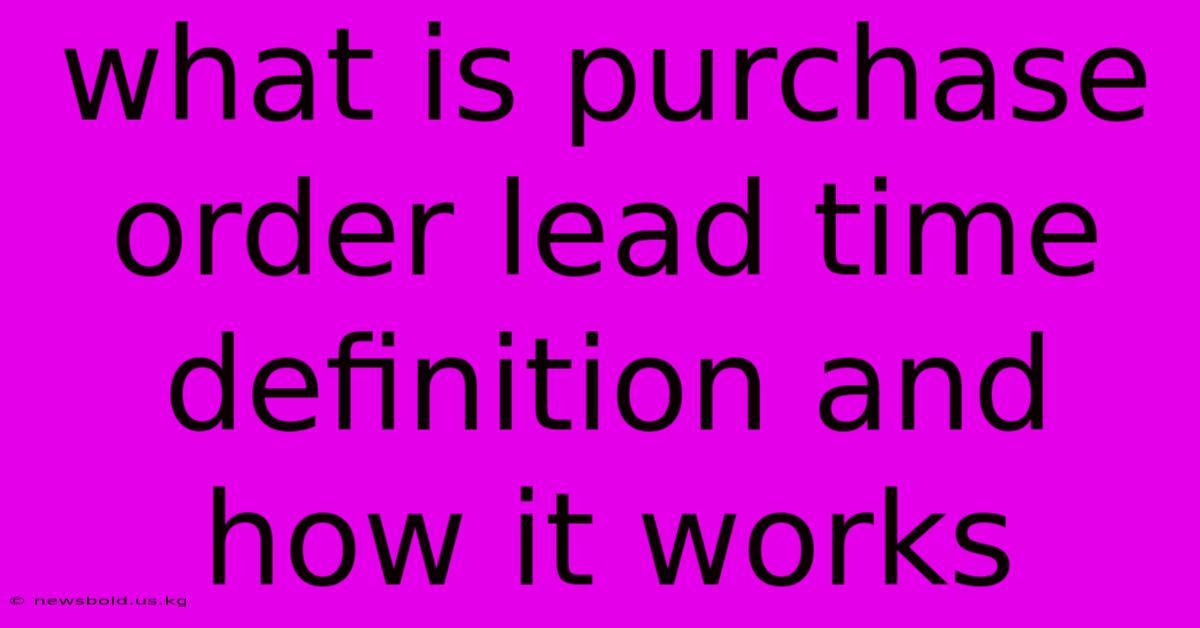
Thank you for taking the time to explore our website What Is Purchase Order Lead Time Definition And How It Works. We hope you find the information useful. Feel free to contact us for any questions, and don’t forget to bookmark us for future visits!
We truly appreciate your visit to explore more about What Is Purchase Order Lead Time Definition And How It Works. Let us know if you need further assistance. Be sure to bookmark this site and visit us again soon!
Featured Posts
-
What Is Credit Life Insurance 3
Jan 09, 2025
-
Why Would Mcdonalds Use Two Joint Ventures To Operate Restaurants In Different Regions Of India
Jan 09, 2025
-
Queuing Theory Definition Elements And Example
Jan 09, 2025
-
How Much Does A Voluntary Repossession Affect Your Credit
Jan 09, 2025
-
What Does Plain Vanilla Mean Definition In Finance
Jan 09, 2025