Quality Management Definition Plus Example
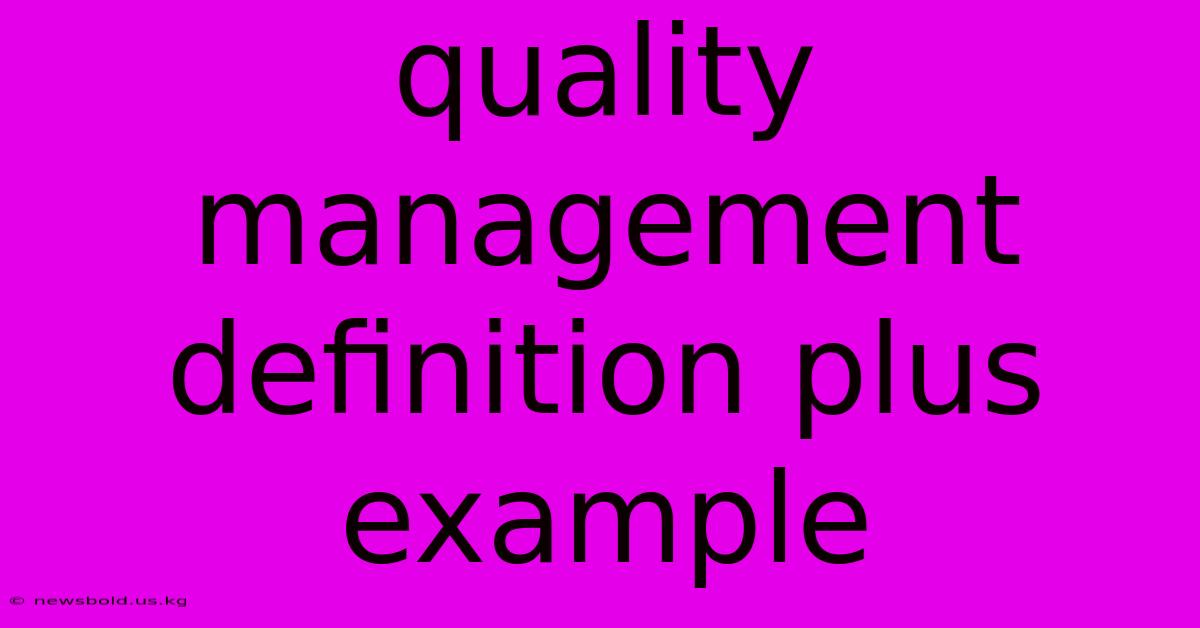
Discover more in-depth information on our site. Click the link below to dive deeper: Visit the Best Website meltwatermedia.ca. Make sure you don’t miss it!
Table of Contents
Unveiling Quality Management: Definitions, Examples, and Best Practices
What defines a truly effective quality management system, and how can organizations leverage it for success? The answer lies in understanding the core principles and practical applications of this crucial business strategy. Quality management is not merely about avoiding defects; it's a proactive approach that fosters continuous improvement and drives exceptional results.
Editor's Note: This comprehensive guide to Quality Management has been published today, offering valuable insights into its definition, practical examples, and impactful benefits.
Why It Matters & Summary: In today's competitive landscape, delivering high-quality products and services is no longer a luxury—it's a necessity. This article provides a detailed exploration of quality management, defining its core concepts and showcasing real-world examples across diverse industries. Understanding quality management principles equips organizations to enhance customer satisfaction, reduce operational costs, improve efficiency, and gain a competitive edge. Key terms covered include quality control, quality assurance, total quality management (TQM), Six Sigma, ISO 9000, and continuous improvement.
Analysis: This guide draws on established quality management frameworks, industry best practices, and case studies to offer a comprehensive understanding of the subject. The analysis integrates diverse perspectives to illustrate the multifaceted nature of quality management and its adaptability across various organizational contexts.
Key Takeaways:
Point | Description |
---|---|
Definition | A systematic approach to ensure products, services, and processes consistently meet or exceed customer expectations. |
Key Principles | Customer focus, leadership commitment, process approach, continuous improvement, data-driven decision making. |
Methods & Tools | Quality control, quality assurance, Six Sigma, TQM, ISO 9000 standards, Kaizen (continuous improvement). |
Benefits | Enhanced customer satisfaction, reduced costs, improved efficiency, increased profitability, competitive advantage. |
Implementation | Requires top management commitment, employee training, clear processes, regular monitoring, and continuous improvement. |
Now, let's delve into the core aspects of quality management.
Quality Management: A Deep Dive
Introduction: Quality management encompasses a range of methodologies and practices aimed at ensuring consistent high quality throughout an organization's operations. It's a holistic approach, impacting everything from product development to customer service.
Key Aspects:
- Quality Planning: Proactive steps to define quality standards, processes, and resources needed to meet customer expectations.
- Quality Control: Monitoring and measuring processes to identify and correct deviations from standards.
- Quality Assurance: Proactive measures to prevent defects and ensure processes consistently meet requirements.
- Quality Improvement: Ongoing efforts to enhance processes, reduce waste, and continuously improve performance.
Quality Planning: Laying the Foundation
Introduction: Effective quality planning forms the bedrock of a robust quality management system. It involves setting clear objectives, defining processes, and allocating resources to achieve those objectives.
Facets:
- Defining Customer Requirements: Understanding customer needs and translating them into specific, measurable quality standards. Example: A car manufacturer might define customer requirements as fuel efficiency, safety features, and comfort.
- Process Mapping: Visualizing the steps involved in producing a product or service to identify potential bottlenecks and areas for improvement. Example: A restaurant might map its order-taking, food preparation, and delivery processes.
- Resource Allocation: Assigning the necessary personnel, equipment, and materials to effectively implement quality plans. Example: A software development company might allocate skilled programmers and testers to a project.
- Risk Assessment: Identifying potential risks that could affect product or service quality and developing mitigation strategies. Example: A pharmaceutical company might assess the risks of contamination during drug production.
Summary: Quality planning lays the foundation for consistent, high-quality outputs by aligning resources and processes with clear, customer-centric objectives.
Quality Control: Monitoring and Correction
Introduction: Quality control focuses on ensuring that outputs conform to predefined standards. This involves monitoring processes, identifying deviations, and implementing corrective actions.
Further Analysis: Quality control is often reactive, addressing problems as they arise. Techniques such as inspection, testing, and statistical process control (SPC) are employed to monitor process performance.
Closing: Effective quality control minimizes defects and ensures that products or services meet quality standards. However, it is often more effective when used in conjunction with proactive quality assurance measures.
Information Table: Common Quality Control Techniques
Technique | Description | Application Examples |
---|---|---|
Inspection | Visual examination or testing to identify defects. | Examining manufactured parts for flaws, reviewing code for bugs. |
Testing | More rigorous evaluation to verify functionality and performance. | Conducting unit tests, system tests, or user acceptance testing. |
Statistical Process Control | Using statistical methods to monitor process variability and identify anomalies. | Tracking production yields, monitoring customer satisfaction scores. |
Quality Assurance: Proactive Prevention
Introduction: Quality assurance focuses on proactive measures to prevent defects and ensure consistent quality. Unlike quality control, which is reactive, quality assurance emphasizes preventing problems before they occur.
Facets:
- Process Design: Designing processes to minimize the potential for errors and defects. Example: Implementing a foolproof system for medication dispensing in a hospital.
- Training & Development: Equipping employees with the skills and knowledge necessary to perform their tasks correctly. Example: Providing training for customer service representatives to handle complaints effectively.
- Documentation: Maintaining detailed records of processes, standards, and quality performance. Example: Creating a detailed instruction manual for assembling a product.
- Continuous Improvement: Regularly reviewing processes and implementing improvements to enhance efficiency and reduce defects. Example: Implementing lean manufacturing principles to eliminate waste in production.
Summary: Quality assurance focuses on establishing robust processes and training to prevent quality issues, leading to improved efficiency and reduced costs.
Quality Improvement: The Continuous Pursuit of Excellence
Introduction: Quality improvement is an ongoing process focused on continuously enhancing performance and achieving greater efficiency. It's a key aspect of building a strong quality management system.
Further Analysis: Various methodologies, including Six Sigma and Lean manufacturing, drive quality improvement. These methodologies employ data-driven approaches to identify and eliminate inefficiencies and defects.
Closing: Continuous improvement is not a one-time activity, but an ongoing commitment to excellence, leading to sustained gains in efficiency and customer satisfaction.
Examples of Quality Management in Action
- Toyota's Production System (TPS): A pioneering approach combining lean principles with quality control to minimize waste and maximize efficiency.
- Six Sigma in Manufacturing: Widely adopted in manufacturing to reduce defects and improve process consistency.
- ISO 9001 Certification: A globally recognized standard demonstrating a company's commitment to quality management.
- Customer Relationship Management (CRM) Systems: Used to track customer feedback and preferences, enhancing product and service design.
FAQ
Introduction: This section addresses common questions regarding quality management.
Questions:
-
Q: What is the difference between quality control and quality assurance?
- A: Quality control is reactive, focusing on identifying and correcting defects. Quality assurance is proactive, focusing on preventing defects through robust processes and training.
-
Q: What are the benefits of implementing a quality management system?
- A: Benefits include improved customer satisfaction, reduced costs, increased efficiency, and a stronger competitive advantage.
-
Q: How can an organization implement a quality management system?
- A: Implementing a QMS requires commitment from top management, employee training, clear procedures, and ongoing monitoring.
-
Q: What are some common quality management tools and techniques?
- A: Common tools include flowcharts, Pareto charts, control charts, and root cause analysis.
-
Q: What is the role of leadership in quality management?
- A: Leadership plays a crucial role in setting the vision, providing resources, and fostering a culture of quality.
-
Q: How can an organization measure the effectiveness of its quality management system?
- A: Effectiveness can be measured using key performance indicators (KPIs) such as defect rates, customer satisfaction scores, and process cycle times.
Summary: Understanding the nuances of quality management is essential for organizational success. Addressing these common questions reinforces the importance of a well-defined QMS.
Tips for Effective Quality Management
Introduction: Implementing a successful quality management system requires a strategic approach. These tips offer practical guidance.
Tips:
- Define clear quality objectives: Establish measurable goals aligned with customer expectations.
- Develop robust processes: Create well-defined, documented processes to minimize errors.
- Implement effective training programs: Ensure employees possess the skills and knowledge to meet quality standards.
- Utilize data-driven decision-making: Track key performance indicators (KPIs) to identify areas for improvement.
- Foster a culture of continuous improvement: Encourage employee participation in identifying and resolving quality issues.
- Regularly review and update the QMS: Ensure the system remains relevant and effective in a changing environment.
- Embrace feedback: Actively solicit and incorporate customer feedback to improve products and services.
- Implement a system of checks and balances: Ensure accountability at all levels of the organization.
Summary: Implementing these tips will build a strong foundation for continuous improvement and sustained success.
Summary: Quality Management – A Strategic Imperative
Quality management is not just a set of procedures; it's a fundamental business strategy that drives efficiency, customer satisfaction, and ultimately, profitability. This comprehensive exploration underscores the importance of proactively addressing quality at every stage of an organization's operations.
Closing Message: By embracing quality management principles and implementing effective strategies, organizations can unlock their full potential, gaining a significant competitive edge in today's demanding market. The journey to quality excellence requires ongoing commitment, but the rewards are immeasurable.
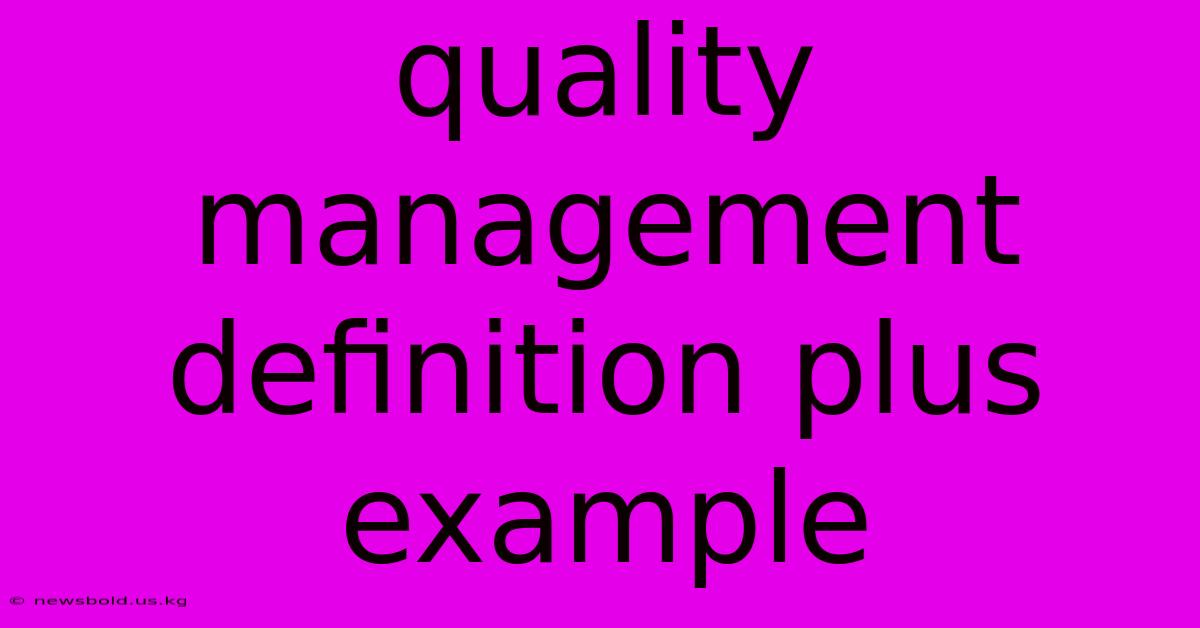
Thank you for taking the time to explore our website Quality Management Definition Plus Example. We hope you find the information useful. Feel free to contact us for any questions, and don’t forget to bookmark us for future visits!
We truly appreciate your visit to explore more about Quality Management Definition Plus Example. Let us know if you need further assistance. Be sure to bookmark this site and visit us again soon!
Featured Posts
-
Prime Underwriting Facility Definition
Jan 09, 2025
-
What Is The Connection Between Goals And Savings
Jan 09, 2025
-
What Special Component Of Risk Is Potentially Greater In Joint Ventures
Jan 09, 2025
-
What Impact Does Labor Migration Between Nations From Joint Ventures Have On The Economics Involved
Jan 09, 2025
-
Recursive Competitive Equilibrium Rce Definition
Jan 09, 2025